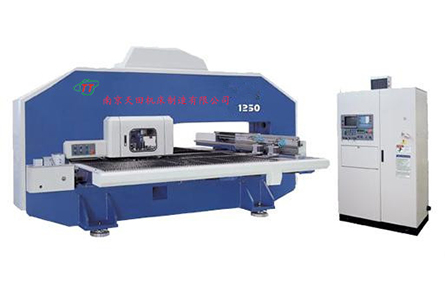
一、HRT系列數(shù)控高精度轉(zhuǎn)塔沖床適用于多種行業(yè),以下是·HRT系列數(shù)控高精度轉(zhuǎn)塔沖床介紹:
數(shù)控高精度轉(zhuǎn)塔沖床:由于需要進(jìn)行模具更換和定位等操作,單個(gè)沖壓動(dòng)作的速度可能不如快速?zèng)_床快。但在加工復(fù)雜零件時(shí),通過(guò)數(shù)控程序控制,能夠?qū)崿F(xiàn)自動(dòng)化連續(xù)加工,減少了人工干預(yù)和模具更換時(shí)間,整體生產(chǎn)效率在加工復(fù)雜工件時(shí)較高。
The CNC high-precision turret punch press has a turret structure. Multiple molds of different shapes and sizes are installed on the turret. Commonly, there are 32 tool heads, 36 tool heads, 48 tool heads, etc., distributed on positions A, B, C, D, and E. Through the control of the rotation of the turret and the movement of the worktable by the numerical control system, the molds can be automatically replaced and the processing positions can be accurately positioned, enabling stamping processing of various shapes and sizes.
The CNC high-precision turret punch press is equipped with a high-precision numerical control system and positioning device. It can precisely control the movement of the worktable and the positioning of the molds, with relatively high processing precision, which can reach ±0.1mm or even higher. It is suitable for the processing of parts with high precision requirements, such as the precision casings of electronic devices and automotive components.
For the CNC high-precision turret punch press, multiple molds can be installed on the turret. It can complete stamping processing of various shapes and sizes in one clamping. It can process complex graphics and hole patterns, with strong flexibility and adaptability. It can process plates of different materials and thicknesses. Generally, the thickness of the plates ranges from about 0.5mm to 12mm.
For the CNC high-precision turret punch press, due to operations such as mold replacement and positioning, the speed of a single stamping action may not be as fast as that of a quick punch press. However, when processing complex parts, through the control of the numerical control program, automated continuous processing can be achieved, reducing manual intervention and mold replacement time, and the overall production efficiency is relatively high when processing complex workpieces
電子電氣行業(yè)
機(jī)箱機(jī)柜:用于加工各類電子設(shè)備的機(jī)箱、機(jī)柜外殼,可在薄板上沖裁出各種形狀的安裝孔、散熱孔、通風(fēng)孔等,以滿足設(shè)備內(nèi)部元件的安裝和散熱需求。
電氣控制箱:對(duì)電氣控制箱的面板進(jìn)行加工,沖制出按鈕孔、指示燈孔、儀表安裝孔等,保證面板的精度和美觀度,同時(shí)提高生產(chǎn)效率。
、汽車制造行業(yè)
車身結(jié)構(gòu)件:能對(duì)汽車車身的各種結(jié)構(gòu)件進(jìn)行加工,如車門內(nèi)板、發(fā)動(dòng)機(jī)艙蓋內(nèi)板、車架縱梁等,通過(guò)沖裁、沖孔等工藝,實(shí)現(xiàn)輕量化設(shè)計(jì)和精確的裝配尺寸要求。
汽車零部件:適用于加工汽車座椅骨架、安全帶固定點(diǎn)、剎車踏板等零部件,能夠在不同厚度的板材上進(jìn)行高精度的沖壓加工,保證零部件的質(zhì)量和性能。
2、機(jī)械制造行業(yè)
工業(yè)設(shè)備外殼:用于制造各類工業(yè)設(shè)備的外殼,如機(jī)床防護(hù)罩、空壓機(jī)外殼、風(fēng)機(jī)外殼等,可根據(jù)設(shè)計(jì)要求沖制出各種形狀的輪廓和孔系,提高外殼的防護(hù)性能和外觀質(zhì)量。
機(jī)械零部件:能加工各種機(jī)械零部件,如齒輪坯、法蘭盤、連接片等,通過(guò)高精度的沖壓工藝,保證零部件的尺寸精度和表面質(zhì)量,為后續(xù)的加工和裝配提供良好的基礎(chǔ)。
建筑裝飾行業(yè)
日常用品行業(yè)
廚具:能對(duì)不銹鋼、鋁板等材質(zhì)的廚具進(jìn)行加工,如鍋具、餐具的沖壓成型,以及在廚具表面沖制出各種花紋、圖案或防滑結(jié)構(gòu)等。
家具五金:適用于加工家具的合頁(yè)、拉手、腳輪等五金配件,通過(guò)沖壓工藝實(shí)現(xiàn)配件的精確成型和批量生產(chǎn),提高生產(chǎn)效率和產(chǎn)品質(zhì)量。
Chassis and Cabinets: It is used to process the chassis and cabinet shells of various electronic devices. It can punch installation holes, heat dissipation holes, ventilation holes, etc. of various shapes on thin plates to meet the installation and heat dissipation requirements of internal components of the devices.
Electrical Control Boxes: It processes the panels of electrical control boxes, punches button holes, indicator light holes, instrument installation holes, etc., ensuring the precision and aesthetic appearance of the panels, and at the same time improving production efficiency.
Body Structural Components: It can process various structural components of automobile bodies, such as inner door panels, inner engine hood panels, frame longitudinal beams, etc. Through processes such as punching and blanking, it can achieve lightweight design and precise assembly dimension requirements.
Automobile Parts: It is suitable for processing automobile parts such as seat frames, seat belt fixing points, brake pedals, etc. It can perform high-precision stamping processing on plates of different thicknesses, ensuring the quality and performance of the parts.
Industrial Equipment Shells: It is used to manufacture the shells of various industrial equipment, such as machine tool protective covers, air compressor shells, fan shells, etc. It can punch out contours and hole systems of various shapes according to design requirements, improving the protective performance and appearance quality of the shells.
Mechanical Parts: It can process various mechanical parts, such as gear blanks, flanges, connecting pieces, etc. Through high-precision stamping processes, it ensures the dimensional accuracy and surface quality of the parts, providing a good foundation for subsequent processing and assembly.
Metal Curtain Walls: It processes the panels of metal curtain walls, punches decorative holes, installation holes of various shapes, as well as special shapes for realizing the shape of the curtain wall to meet the design requirements of the building's appearance.
Ceilings: It can process various styles of ceilings, such as punched sound-absorbing ceilings, shaped ceilings, etc. Through the high-precision processing of the punch press, it ensures the flatness of the ceiling and the consistency of the hole patterns, improving the decorative effect.
Kitchenware: It can process kitchenware made of materials such as stainless steel and aluminum plates, such as the stamping and forming of pots and tableware, and punching out various patterns, designs or anti-slip structures on the surface of the kitchenware.
Furniture Hardware: It is suitable for processing furniture hardware accessories such as hinges, handles, and casters. Through the stamping process, it realizes the precise forming and mass production of the accessories, improving production efficiency and product quality
三、HRT系列數(shù)控高精度轉(zhuǎn)塔沖床的工作原理如下:
動(dòng)力傳動(dòng)原理:通過(guò)電機(jī)驅(qū)動(dòng)飛輪,飛輪儲(chǔ)存能量并在沖壓時(shí)釋放,經(jīng)離合器和傳動(dòng)機(jī)構(gòu)將動(dòng)力傳遞到?jīng)_頭。當(dāng)離合器接合,飛輪帶動(dòng)曲軸旋轉(zhuǎn),曲軸通過(guò)連桿使沖頭做上下往復(fù)運(yùn)動(dòng),實(shí)現(xiàn)沖壓動(dòng)作。
數(shù)控系統(tǒng)控制原理:操作人員在數(shù)控系統(tǒng)中輸入加工指令,包括沖壓位置、沖壓次數(shù)、模具選擇等信息。數(shù)控系統(tǒng)依據(jù)這些指令,精確控制伺服電機(jī)驅(qū)動(dòng)工作臺(tái)和轉(zhuǎn)塔的運(yùn)動(dòng)。例如,工作臺(tái)在 X、Y 軸方向上的移動(dòng)由伺服電機(jī)通過(guò)滾珠絲杠副來(lái)實(shí)現(xiàn),能精準(zhǔn)定位板材,使沖壓位置符合設(shè)計(jì)要求;轉(zhuǎn)塔的旋轉(zhuǎn)由伺服電機(jī)帶動(dòng),可快速準(zhǔn)確地選擇所需模具。
模具工作原理:轉(zhuǎn)塔沖床的轉(zhuǎn)塔上安裝有多個(gè)不同形狀和尺寸的模具。當(dāng)需要進(jìn)行沖壓加工時(shí),數(shù)控系統(tǒng)控制轉(zhuǎn)塔旋轉(zhuǎn),將選定的模具對(duì)準(zhǔn)沖頭。沖頭下行時(shí),模具對(duì)板材施加壓力,使板材在模具的作用下產(chǎn)生塑性變形,從而沖剪出所需的形狀和孔型。
The flywheel is driven by the motor. The flywheel stores energy and releases it during stamping. The power is transmitted to the punch through the clutch and the transmission mechanism. When the clutch engages, the flywheel drives the crankshaft to rotate. The crankshaft makes the punch move up and down reciprocally through the connecting rod to achieve the stamping action.
The operator inputs processing instructions into the CNC system, including information such as stamping positions, the number of stamping times, and mold selection. Based on these instructions, the CNC system precisely controls the movement of the worktable and the turret driven by the servo motor. For example, the movement of the worktable in the X and Y axis directions is realized by the servo motor through the ball screw pair, which can accurately position the sheet metal so that the stamping position meets the design requirements. The rotation of the turret is driven by the servo motor, which can quickly and accurately select the required mold.
Multiple molds of different shapes and sizes are installed on the turret of the turret punch press. When stamping processing is required, the CNC system controls the rotation of the turret to align the selected mold with the punch. When the punch moves downward, the mold applies pressure to the sheet metal, causing the sheet metal to undergo plastic deformation under the action of the mold, thereby punching out the required shapes and hole patterns
四、HRT系列數(shù)控高精度轉(zhuǎn)塔沖床性能特點(diǎn):
◆液壓系統(tǒng),數(shù)字式比例伺服閥全閉環(huán)控制,分辨率高,行程、速度數(shù)字可調(diào)。
◆沖壓速度1000HPM;精確控制下死點(diǎn),極為方便的加工百頁(yè)窗、敲落孔、滾筋、滾剪、壓印等。
◆鑲套并成對(duì)加工的轉(zhuǎn)盤,保證上下模的同軸度。
◆配套的氣動(dòng)、液壓及電氣元件,保證整機(jī)性能的可靠性。
◆智能夾鉗,可根據(jù)加工板材情況自動(dòng)移動(dòng)位置,使加工無(wú)死區(qū)。
◆真空吸廢裝置,保證高速?zèng)_裁時(shí)廢料準(zhǔn)確落下,徹底消除廢料反彈,延長(zhǎng)模具壽命。
◆大導(dǎo)程滾珠絲杠、直線導(dǎo)軌,保證加工精度。
◆鋼板焊接的閉式O型機(jī)身,剛性好,變形小。
◆夾鉗自動(dòng)保護(hù),保護(hù)區(qū)域內(nèi)不沖壓,避免模具、夾鉗受損,保證程序運(yùn)轉(zhuǎn)持續(xù)性。
◆旋轉(zhuǎn)工位采用高精度渦輪、蝸桿機(jī)構(gòu),分度精度極高,最大直徑φ88.9,并可擴(kuò)展。
◆自動(dòng)集中潤(rùn)滑裝置,減少各運(yùn)動(dòng)付的摩擦,提高機(jī)器使用壽命。
◆整體式橫梁結(jié)構(gòu),拖板與橫梁一體化設(shè)計(jì),增強(qiáng)剛性,定位準(zhǔn)確,高速送料更平穩(wěn),杜絕工作臺(tái)X、 Y軸動(dòng)態(tài)偏移情況。
The hydraulic system is controlled by a digital proportional servo valve in a full closed-loop mode, featuring high resolution, and the stroke and speed can be adjusted digitally.
The stamping speed can reach 1000 HPM. It can precisely control the bottom dead center, making it extremely convenient for processing louver windows, knockout holes, rolling beads, roll shearing, embossing, etc.
The turntable with inserted sleeves and processed in pairs ensures the coaxiality of the upper and lower molds.
The supporting pneumatic, hydraulic and electrical components ensure the reliability of the overall machine performance.
The intelligent clamp can automatically move according to the situation of the processed sheet metal, eliminating the dead zone during processing.
The vacuum waste suction device ensures that the waste falls accurately during high-speed blanking, completely eliminating waste bounce and extending the service life of the mold.
The large lead ball screw and linear guide ensure the processing accuracy.
The closed O-shaped body made of welded steel plates has good rigidity and small deformation.
The automatic protection of the clamp prevents stamping within the protected area, avoiding damage to the mold and clamp and ensuring the continuity of the program operation.
The rotating station adopts a high-precision turbine and worm mechanism with extremely high indexing accuracy. The maximum diameter is φ88.9 and can be expanded.
The automatic centralized lubrication device reduces the friction of each moving pair and improves the service life of the machine.
The integral beam structure, with the design of the carriage integrated with the beam, enhances the rigidity, ensures accurate positioning, makes the high-speed feeding more stable, and eliminates the dynamic offset of the X and Y axes of the worktable
五、HRT系列數(shù)控高精度轉(zhuǎn)塔沖床常用設(shè)備的部分技術(shù)參數(shù)
參數(shù)名稱 | 單位 | 小型機(jī) | 中型機(jī) | 大型機(jī) |
---|
公稱壓力 | kN | 160 - 250 | 315 - 400 | 400 - 630 |
喉口深度 | mm | 300 - 400 | 400 - 500 | 500 - 600 |
滑塊行程 | mm | 30 - 50 | 40 - 60 | 50 - 80 |
最大開啟高度 | mm | 250 - 350 | 350 - 450 | 450 - 600 |
主電機(jī)功率 | kW | 11 - 18.5 | 18.5 - 30 | 30 - 45 |
數(shù)控系統(tǒng) | - | FANUC 0i - MD | SIEMENS 840D | HEIDENHAIN TNC640 |
工位數(shù)量 | 個(gè) | 12 - 16 | 16 - 24 | 24 - 32 |
工位類型 | - | 標(biāo)準(zhǔn) + 大工位 | 標(biāo)準(zhǔn) + 大 + 旋轉(zhuǎn) | 標(biāo)準(zhǔn) + 大 + 旋轉(zhuǎn) |
刀庫(kù)容量 | 套 | 12 - 16 | 16 - 24 | 24 - 32 |
模具尺寸范圍 | mm | φ32 - φ100 | φ32 - φ125 | φ50 - φ150 |
設(shè)備外形尺寸 | m | 3.5×2.2×2.5 | 4.5×2.8×2.8 | 6.0×3.2×3.0 |
重量 | t | 5 - 8 | 8 - 12 | 12 - 20 |
定位精度 | mm | ±0.05/300 | ±0.03/300 | ±0.02/300 |
重復(fù)定位精度 | mm | ±0.03 | ±0.02 | ±0.015 |
最大沖壓速度 | SPM | 300 - 500 | 250 - 400 | 200 - 350 |
板材最大厚度 | mm | 6 - 8 | 8 - 12 | 12 - 16 |
V、Partial technical parameters of common equipment of the HRT series CNC high-precision turret punch pressParameter Name | Unit | Small-sized Machine | Medium-sized Machine | Large-sized Machine |
---|
Nominal Pressure | kN | 160 - 250 | 315 - 400 | 400 - 630 |
Throat Depth | mm | 300 - 400 | 400 - 500 | 500 - 600 |
Slide Stroke | mm | 30 - 50 | 40 - 60 | 50 - 80 |
Maximum Opening Height | mm | 250 - 350 | 350 - 450 | 450 - 600 |
Main Motor Power | kW | 11 - 18.5 | 18.5 - 30 | 30 - 45 |
CNC System | - | FANUC 0i - MD | SIEMENS 840D | HEIDENHAIN TNC640 |
Number of Stations | - | 12 - 16 | 16 - 24 | 24 - 32 |
Station Type | - | Standard + Large Station | Standard + Large + Rotating Station | Standard + Large + Rotating Station |
Tool Magazine Capacity | Set | 12 - 16 | 16 - 24 | 24 - 32 |
Mold Size Range | mm | φ32 - φ100 | φ32 - φ125 | φ50 - φ150 |
Overall Dimensions of Equipment | m | 3.5×2.2×2.5 | 4.5×2.8×2.8 | 6.0×3.2×3.0 |
Weight | t | 5 - 8 | 8 - 12 | 12 - 20 |
Positioning Accuracy | mm | ±0.05/300 | ±0.03/300 | ±0.02/300 |
Repeated Positioning Accuracy | mm | ±0.03 | ±0.02 | ±0.015 |
Maximum Stamping Speed | SPM | 300 - 500 | 250 - 400 | 200 - 350 |
Maximum Thickness of Sheet Metal | mm | 6 - 8 | 8 - 12 | 12 - 16 |
六、常用設(shè)備配置說(shuō)明
傳動(dòng)系統(tǒng)
刀庫(kù)分布
標(biāo)準(zhǔn)工位:φ32mm(常用模具)
大工位:φ100 - φ125mm(成型模、拉伸模)
旋轉(zhuǎn)工位:支持 360° 任意角度旋轉(zhuǎn)(用于切角、百葉窗等)
液壓系統(tǒng)
系統(tǒng)壓力:16 - 25MPa
油泵流量:20 - 40L/min
油箱容量:200 - 400L
電氣系統(tǒng)
可選配置
自動(dòng)上下料系統(tǒng)
激光尋邊裝置
模具快速更換系統(tǒng)
遠(yuǎn)程監(jiān)控系統(tǒng)
VI. Instructions for the Configuration of Common Equipment
Transmission System
Tool Magazine Distribution
Standard Station: φ32mm (Commonly used molds)
Large Station: φ100 - φ125mm (Forming molds, drawing molds)
Rotating Station: Supports 360° rotation at any angle (Used for cutting corners, louver windows, etc.)
Hydraulic System
System Pressure: 16 - 25MPa
Oil Pump Flow Rate: 20 - 40L/min
Oil Tank Capacity: 200 - 400L
Electrical System
Control Voltage: AC 380V/50Hz
Control Mode: Full closed-loop control
Safety Protection: Overload protection, light curtain protection, emergency stop
Optional Configurations
Remarks: The above parameters are typical values, and the actual specifications may vary depending on the manufacturer and model. When selecting a model, customization should be carried out according to specific processing requirements (material thickness, processing accuracy, production efficiency).
備注:以上參數(shù)為典型值,實(shí)際規(guī)格可能因制造商和型號(hào)而異。選型時(shí)需根據(jù)具體加工需求(材料厚度、加工精度、生產(chǎn)效率)進(jìn)行定制。
Remarks: The above parameters are typical values, and the actual specifications may vary depending on the manufacturer and model. When selecting a model, customization is required according to specific processing requirements (material thickness, processing accuracy, production efficiency)。